The term “quality” holds various meanings for different individuals. While it is commonly used, the concept and terminology associated with quality can be quite ambiguous. When asked to define “quality,” one might receive a wide range of responses.
The interpretation of quality frequently varies among stakeholders, who are individuals with a vested interest in the process. In the context of manufacturing, quality can be defined in a relatively clear manner: products should function as intended, with minimal faults or failures. This principle is applicable to both products and services.
Definitions of quality rooted in manufacturing primarily focus on engineering and production practices, adhering to the universal standard of “conformance to requirements.” These requirements, or specifications, are predetermined designs, and any deviation from them signifies a decline in quality. In service sectors, however, customer satisfaction often serves as the main indicator of quality.
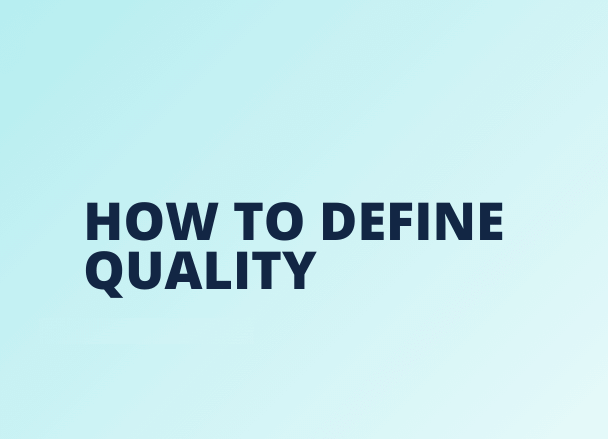
A contemporary understanding of quality is encapsulated in Juran’s concept of “fitness for intended use,” which suggests that quality involves “meeting or exceeding customer expectations.” According to Deming, the customer’s perspective on quality is the only one that truly matters.
Excellence in quality is not solely determined by individual perception but is instead defined by the standards established by the organization. This perspective, however, has notable shortcomings. The consumer’s understanding of quality is often linked to conformity, which results in an inward focus. A strong emphasis on reliability in both design and manufacturing typically prioritizes cost reduction as the main goal. This approach to cost reduction is often narrowly defined, focusing on investing in design and manufacturing enhancements until the incremental costs align with the expenses associated with non-quality issues, such as rework or waste.
In the realm of manufacturing, excellence is characterized by the absence of defects, deficiencies, and significant variations, achieved through strict and consistent adherence to measurable and verifiable standards. This ensures uniform output that meets specific customer or user requirements. According to the ISO 8402-1986 standard, quality is defined as “the totality of features and characteristics of a product or service that bear its ability to satisfy stated or implied needs.”
The Baldrige Criteria does not explicitly use the term quality, as every action and decision within its framework is inherently a quality-related activity or decision. This premise suggests that quality is ingrained in the very essence of the organization, representing the ideal approach to conducting business.
While quality holds significant importance for businesses, it can be challenging to define. The interpretation of quality varies based on context and perception. For instance, the concept of quality differs when considering tangible products compared to the perception of a quality service. Additionally, the understanding of quality can be influenced by time and situational factors.
Let us put forth a question to you that is worth pondering from time to time: How would you effectively articulate the concept of Quality?